A second, constructive life for greenhouse gas
Hong Kong's eco-bricks lay foundation for cleaner future

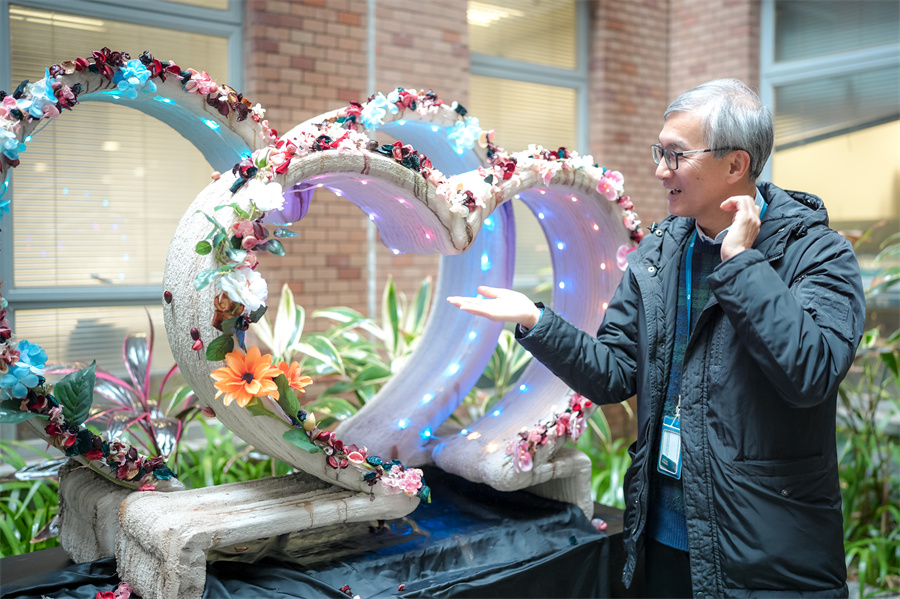
Application struggle
Despite the optimism, these technologies are still struggling to find their way to commercialization, according to Poon Chi-sun. Poon, director of the Research Centre for Resources Engineering Towards Carbon Neutrality at the Hong Kong Polytechnic University, is the unsung hero behind the city's wide use of eco-bricks.
Traditional eco-bricks, made from recycled glass and construction debris, have been used in public footpaths since 2010, after the government mandated that recycled glass cullet contribute 20 to 25 percent of the weight to eco-pavers in road maintenance contracts.
In 2024, a total of 178,000 square meters of eco-pavers were used in public works, almost triple the 64,000 square meters in 2020, according to the government.
Since the 1990s, Poon has steadily improved his eco-bricks, which are now in their fifth generation. However, their application has stalled at the second generation.
Despite their potential to address roadside air pollution, third-generation eco-bricks have struggled to gain market traction. They include titanium dioxide photocatalysts, which react with sunlight to reduce air pollutants like nitrogen oxide, kill bacteria, and self-clean.
Poon said, with government support, it took a decade for the city to adopt the second-generation eco-bricks.
To spearhead the promotion and commercialization of low-carbon construction materials and carbon capturing technology, Poon co-founded Carbon Capture & Storage Limited with colleagues.
One of the key patents the company holds is low-carbon concrete, which uses sea mud or recycled waste such as glass, incineration bottom ash and coal ash, to replace the use of cement. "Producing one ton of cement releases 0.8 tons of carbon dioxide," Poon said.
Many construction materials can absorb carbon dioxide. For example, cement contains calcium, which reacts with CO2 to form calcium carbonate. This inspired Poon to use CO2 for curing, a process that makes freshly laid concrete and other materials stronger and more durable.
Standard concrete curing takes 28 days, but CO2 can speed the process up. Placing fresh concrete or bricks in a carbon dioxide-rich room absorbs the gas, accelerates curing, and enhances durability.
Given Hong Kong's focus on building safety and its cautious regulatory approach to innovative materials, Poon, who is nearing retirement, said it could take 15 to 20 years for the new material to gain widespread acceptance.
One stumbling block is Hong Kong's lack of construction material manufacturing, with only a few cement producers.
"Most materials are made on the mainland. With the widespread use of Modular Integrated Construction, many are prefabricated there and shipped to Hong Kong," Poon said.
Cost-effectiveness is also a challenge to finding investors. Despite its low-carbon benefits, the new technology offers uncertain immediate returns.